The PHG135 type dry-way extruder is mainly used in producing of expanded soybean and corn etc.
This extruding machine is possessed of cooking, sterilizing, extruding, dewatering and stabilizing treatment functions. Application of extrusion technology is the new direction of feed industry development.
This machine adopts dry-way extrusion technology, simple technology and wide adaptability. By using self-heating method, the material can be cooked to 130~150 ℃ without conditioner and boiler unit. The extruded material can be long-term stored with properly water content. The material can be packed after cooling treatment. Step-less speed regulation makes this type machine stand out for the easy operation, compact conformation and reliable performance.
PHG135 type extruding machinery is composed of hopper, positive displacement screw feeding device, water adding system, extruding chamber, cutting device (select), drive mechanism and machine frame.
Being an important part of feed extruder, extruding chamber is composed of main shaft, extruding screw rod, tapered pressure ring, wear ring and extruding sleeve. The extruding screw rod adopts segmental structure, equal diameter and variable pitch form to meet the demand for flexible assemble of different screw rods according to different raw materials. Configure the tapered pressure rings with different diameters to adjust and control the temperature and pressure in the chamber during extruding process. The extruding sleeve is composed of a feeding extruding chamber part, two middle extruding chamber parts and a discharging extruding chamber.
9/25/2013
9/24/2013
Production Process with Paddle Mixer
The SJHS2A Double-circle Paddle Mixer is widely used for mixing powdery and special granular materials in feed industry. Mixing machine is playing a vital role in feed production. It is fair to say that if proportioning system is disjoined from mixer, even with advanced manufacturing processes, the production will become meaningless. Therefore, the quality and performance of mixing machine directly influences survival and development of feed mills. Stable-performance equipment not only helps enterprises to keep making profits but also reduce large sum of money for maintenance and repairing.
(1) Feeding
Solid materials
The materials can be directly fed from the bin (see Fig.2-7 005) controlled by a lock gate (see Fig.2-7 006) after weighting with the proportion scales (see Fig. 2-7 001), and also can be fed via a covering equipment or via an operator (see Fig.2-3 003) at the manual dumping bit (see Fig.2-7 004).
Liquid (if necessary)
Liquid is generally fed into the mixing machine via the liquid addition system (see Fig. 2-7 010).
(2) Discharging
The mixtures conveyed from mixer (see Fig. 2-7 007) shall be collected by a surge bin (see Fig. 2-7 008);
And the volume of surge bin should be 1.5 times more than that of feed mixer. The surge bin usually has an access door (manhole) and a glass inspection window; the lower part shall have a lock gate or conveying equipment (see Fig. 2-7 009);
The upper end of air-return duct (see Fig. 2-7 009) is connected to the surge bin or that above the scale to ensure stably feeding. In addition, the surge bin shall be removable for maintainability; the environmental protection equipment can be equipped at the outlet to prevent dust pollution of the surge bin.


(1) Feeding
Solid materials
The materials can be directly fed from the bin (see Fig.2-7 005) controlled by a lock gate (see Fig.2-7 006) after weighting with the proportion scales (see Fig. 2-7 001), and also can be fed via a covering equipment or via an operator (see Fig.2-3 003) at the manual dumping bit (see Fig.2-7 004).
Liquid (if necessary)
Liquid is generally fed into the mixing machine via the liquid addition system (see Fig. 2-7 010).
(2) Discharging
The mixtures conveyed from mixer (see Fig. 2-7 007) shall be collected by a surge bin (see Fig. 2-7 008);
And the volume of surge bin should be 1.5 times more than that of feed mixer. The surge bin usually has an access door (manhole) and a glass inspection window; the lower part shall have a lock gate or conveying equipment (see Fig. 2-7 009);
The upper end of air-return duct (see Fig. 2-7 009) is connected to the surge bin or that above the scale to ensure stably feeding. In addition, the surge bin shall be removable for maintainability; the environmental protection equipment can be equipped at the outlet to prevent dust pollution of the surge bin.
9/23/2013
Top-notch Steel Structure Engineering from Muyang
Since its founding in 1996, Muyang Steel Structure Co. Ltd has been committed to spearheading development of steel structure technology with consistent technical innovation and meticulous product management. Its scope of business covers design, structural steel fabrication and installation of civil steel structure buildings, tunnel and bridge steel structure for transportation facilities.
The company now employs over 100 technical staff and owns fixed assets of RMB 50000000 including over 200 units of world-advanced capital equipment. With long-term good business relations with many well-known companies including Hope Group(Sicuan), Tongwei Group(Sicuan), Yangzhou CIMC Tonghua Special Vehicles Co.,Ltd., Liuhe Group(Shandong), Suning Group, Jiangsu Sanxiao Group, CSC Group, Jiangsu Chengde Steel Pipe Co.Ltd, Anhui Jiatong Group, China Railway First Group Co. Ltd., China Railway Eighteenth Group Co.Ltd,. China Petroleum Pipeline and Equioment Corporation, Nanjing Dadi Construction Group, CJ Liaocheng Co., Yangzhou Yongfeng Paper Company and so on, Muyang Steel Structure Co. Ltd. has completed over 1000 steel structure buildings and projects in China and export to USA, Japan, Australia, Russia, Sadui Arabia, and many other countries.
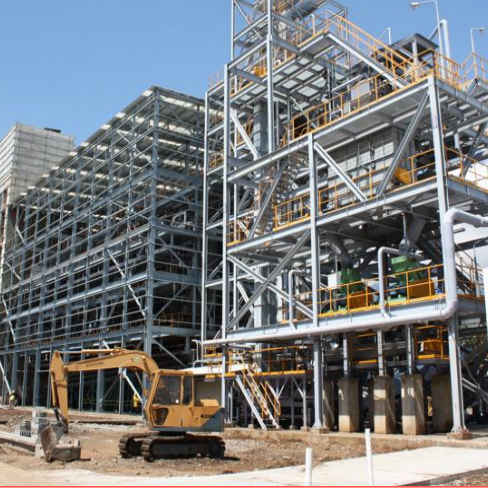
In keeping with its corporate sprit featuring innovation, responsibility, cooperation and efficiency, Muyang Steel Structure Co. Ltd. will continue its perseverant efforts aimed at "laying a solid foundation for a century's glory by creating a world-class brand". Muyang steel structure engineering features:
1. Design and construction at the national first-level with qualification;
2. Involved with steel architecture designing, fabricating and installing;
3. Thousands of steel structure engineering and project contracting experience;
4. Global service network system.
The company now employs over 100 technical staff and owns fixed assets of RMB 50000000 including over 200 units of world-advanced capital equipment. With long-term good business relations with many well-known companies including Hope Group(Sicuan), Tongwei Group(Sicuan), Yangzhou CIMC Tonghua Special Vehicles Co.,Ltd., Liuhe Group(Shandong), Suning Group, Jiangsu Sanxiao Group, CSC Group, Jiangsu Chengde Steel Pipe Co.Ltd, Anhui Jiatong Group, China Railway First Group Co. Ltd., China Railway Eighteenth Group Co.Ltd,. China Petroleum Pipeline and Equioment Corporation, Nanjing Dadi Construction Group, CJ Liaocheng Co., Yangzhou Yongfeng Paper Company and so on, Muyang Steel Structure Co. Ltd. has completed over 1000 steel structure buildings and projects in China and export to USA, Japan, Australia, Russia, Sadui Arabia, and many other countries.
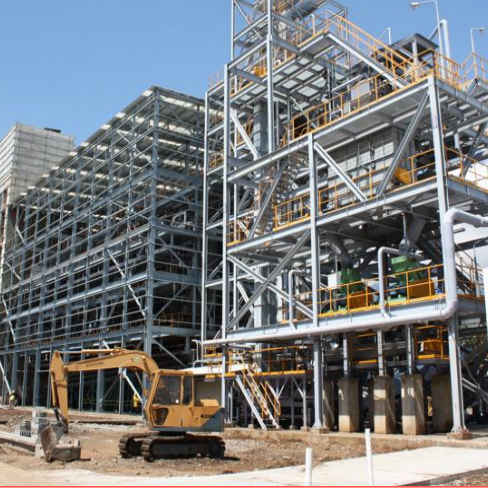
In keeping with its corporate sprit featuring innovation, responsibility, cooperation and efficiency, Muyang Steel Structure Co. Ltd. will continue its perseverant efforts aimed at "laying a solid foundation for a century's glory by creating a world-class brand". Muyang steel structure engineering features:
1. Design and construction at the national first-level with qualification;
2. Involved with steel architecture designing, fabricating and installing;
3. Thousands of steel structure engineering and project contracting experience;
4. Global service network system.
9/22/2013
Main Motor and Rotor Assembly for MUZL 610TW Type Pellet Mill
Main motor
This type of pelleting machine includes two main motors, which are symmetrically installed at both sides of the pellet mill.
The two motors shall rotate in the same direction and finally the ring die shall rotate in clockwise.
The two motors shall startup in star form at the same time, while under normal operation speed the one is transmitted to a triangle connection firstly, and the other also to a triangle operation about five seconds later.
Two motors must run at a same direction and commissioned separately before commissioning and starting of this machine.
Rotor assembly
Main components of rotor assembly are shown in Fig 2.3.
The oil-way of rotor assembly shall be kept unobstructed, after filling the oil from oil nozzle of distributer at rear end, the lubricating oil leading to press roller bearings shall overflow from the seal plate at the end of the press roller after being filled up, and lubricating oil leading to rotor bearings shall overflow from the clearance between the rotor and main shaft disc after being filled up.(It is guaranteed by the oil seal installation direction of the rotor)
Generally, in good lubrication, the service life of the bearings and oil seals of the rotor are longer and they are uneasy to be damaged. It is suggested to ask pellet mill experts of Muyang Group for guide when replacing bearings and oil seals.
Pay attention to abrasion of the cone face of driving flange of the ring die, see Section 7.5 for assembling and disassembling as well as maintenance.

Shear pin assembly
The main parts of the shear pin assembly are shown as Fig.2.5.
When there is large iron block or other impurities entering between the ring die and press roller, in which case, the toque delivered by main shaft will exceed the shear force of the shear pin (part 3), and the shear pin will be sheared off and drove the main shaft rotating with the rotor, the limit switch (part 5) will be cut off to stop the main motor, and take the effect of protecting ring die and press roller.
Restore the Shear pin disc (part 2) to replace a new shear pin after it is sheared off.
This type of pelleting machine includes two main motors, which are symmetrically installed at both sides of the pellet mill.
The two motors shall rotate in the same direction and finally the ring die shall rotate in clockwise.
The two motors shall startup in star form at the same time, while under normal operation speed the one is transmitted to a triangle connection firstly, and the other also to a triangle operation about five seconds later.
Two motors must run at a same direction and commissioned separately before commissioning and starting of this machine.
Rotor assembly
Main components of rotor assembly are shown in Fig 2.3.
The oil-way of rotor assembly shall be kept unobstructed, after filling the oil from oil nozzle of distributer at rear end, the lubricating oil leading to press roller bearings shall overflow from the seal plate at the end of the press roller after being filled up, and lubricating oil leading to rotor bearings shall overflow from the clearance between the rotor and main shaft disc after being filled up.(It is guaranteed by the oil seal installation direction of the rotor)
Generally, in good lubrication, the service life of the bearings and oil seals of the rotor are longer and they are uneasy to be damaged. It is suggested to ask pellet mill experts of Muyang Group for guide when replacing bearings and oil seals.
Pay attention to abrasion of the cone face of driving flange of the ring die, see Section 7.5 for assembling and disassembling as well as maintenance.

Shear pin assembly
The main parts of the shear pin assembly are shown as Fig.2.5.
When there is large iron block or other impurities entering between the ring die and press roller, in which case, the toque delivered by main shaft will exceed the shear force of the shear pin (part 3), and the shear pin will be sheared off and drove the main shaft rotating with the rotor, the limit switch (part 5) will be cut off to stop the main motor, and take the effect of protecting ring die and press roller.
Restore the Shear pin disc (part 2) to replace a new shear pin after it is sheared off.

9/18/2013
MUZL610 Series Pellet Mill
MUZL610-type pellet mill is an advanced pellet mill, which is of Jiangsu Muyang Group manufactured. The entire manufacturing process is in full accordance with international technical standards.
Application and adaptability
(1) This pellet mill is specially used for animal feed processing, generally for processing powdery, foldable and easily pelletized materials.
(2) For ensuring the operation safety of the machine, the altitude of the service region of this machine should be less than 1000m, temperature range 5℃~40℃, and air relative humidity range 30%~ 85%.
(3) Do not used in food processing.
(4) When the region does not accord with the above conditions, in order to be given special instructions.
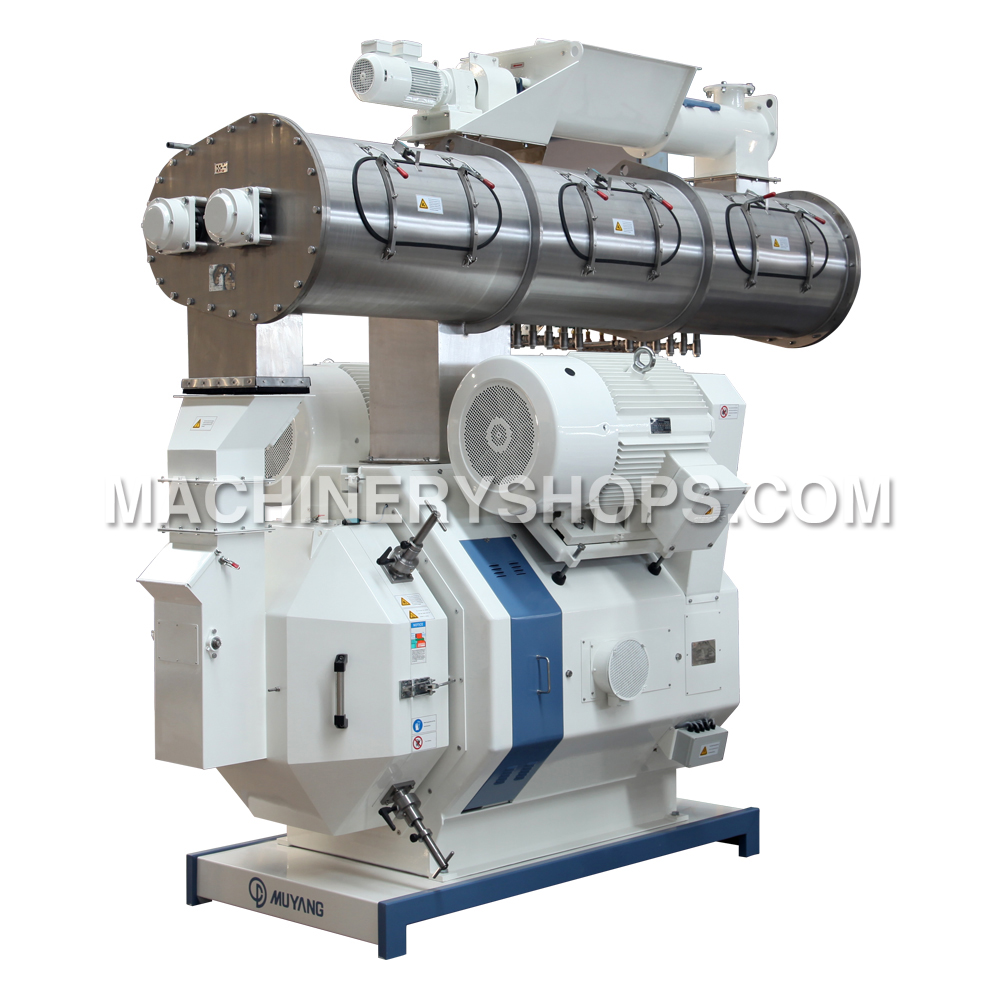
Main features and functions of the equipment
(1) MUZL610-type pelleting machine is an advanced pellet mill, which is of Jiangsu Muyang Group manufactured. The entire manufacturing process is in full accordance with international technical standards.
(2) Double-motor and V-belt driving system is adopted for this machine type, which is characterized by ideal drive ratio, great driving moment, smooth rotation, high output, low noise, and easy operation and maintenance.
(3) This type of machine can be fitted with many kinds of ring dies with φ1.5~ φ12 die holes and different thickness, so customers can select them for use as required to achieve the optimum technical and economic efficiency.
(4) Advanced frequency control motor is adopted for this machine type to feed material, equipped with overload protection devices, outside discharging mechanisms and Magnetic separating device.
(5) Various conditioners are available, such as single-conditioner, double-conditioner, triple-conditioner, different diameter cylinder conditioner and feed etc.
Application and adaptability
(1) This pellet mill is specially used for animal feed processing, generally for processing powdery, foldable and easily pelletized materials.
(2) For ensuring the operation safety of the machine, the altitude of the service region of this machine should be less than 1000m, temperature range 5℃~40℃, and air relative humidity range 30%~ 85%.
(3) Do not used in food processing.
(4) When the region does not accord with the above conditions, in order to be given special instructions.
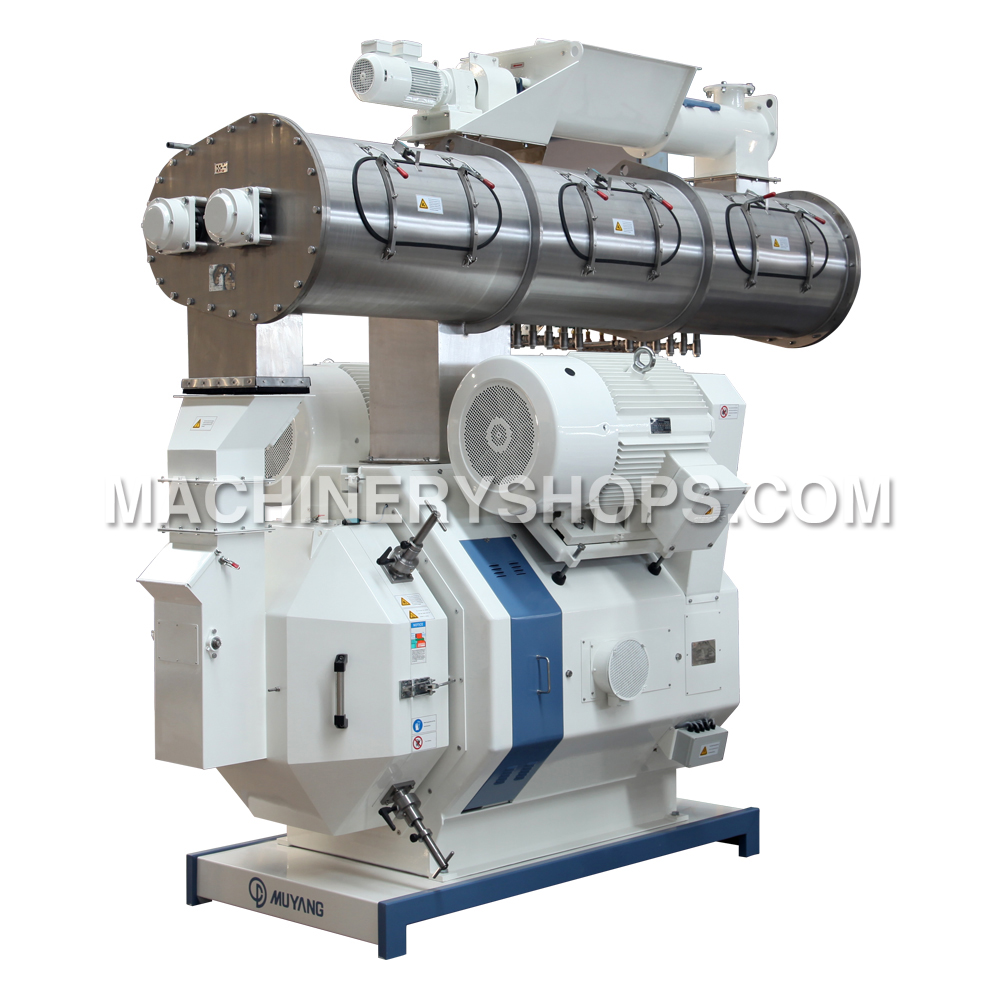
Main features and functions of the equipment
(1) MUZL610-type pelleting machine is an advanced pellet mill, which is of Jiangsu Muyang Group manufactured. The entire manufacturing process is in full accordance with international technical standards.
(2) Double-motor and V-belt driving system is adopted for this machine type, which is characterized by ideal drive ratio, great driving moment, smooth rotation, high output, low noise, and easy operation and maintenance.
(3) This type of machine can be fitted with many kinds of ring dies with φ1.5~ φ12 die holes and different thickness, so customers can select them for use as required to achieve the optimum technical and economic efficiency.
(4) Advanced frequency control motor is adopted for this machine type to feed material, equipped with overload protection devices, outside discharging mechanisms and Magnetic separating device.
(5) Various conditioners are available, such as single-conditioner, double-conditioner, triple-conditioner, different diameter cylinder conditioner and feed etc.
9/17/2013
Installation of Bridge-breaking Feeding Bin and Feeder
One of basic reference data for the control system of the extruder is the material flow rate, and the addition level of water, steam and other liquids in the system shall refer to the material flow rate, therefore the stability of material flow will directly affect that of the whole extruder producing. To ensure stable materials flow, weighing feeding is used in this system, namely, put the whole feeding bin and feeder onto the weighing sensor, so as to form a closed-loop control among weighing sensor, frequency-converted feeder and computer, and then realize feeding.
A basic requirement to the weighing feeding of the feed extruder is a flexible connection between upper and lower interface, namely, the flexible connection between bridge-breaking feeding bin and pneumatic gate at upper part of the bin, as well as the flexible connection between feeder outlet and conditioner inlet, canvas is usually used as the material for flexible connection for this two parts.
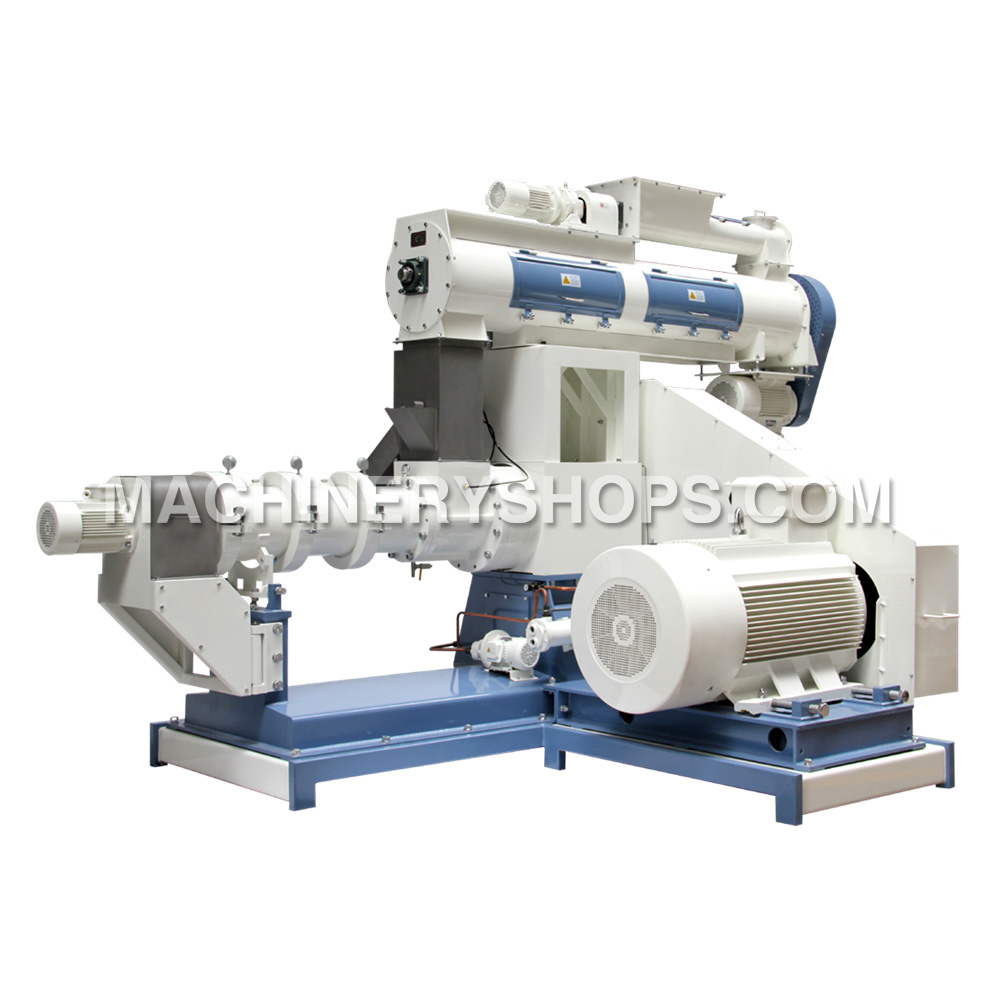
Installation of weighing sensor is another important factor affecting the feeding. There are generally two methods for sensor installation: hanging installation and supporting installation, which will be used as required in the site. Necessary measures shall be taken to ensure stability of bin body while hanging installation is used. During production of extruding machine, falling down of materials, when feeding to the feeding bin, will make the whole bin body waggled, the waggling extent and time will closely related to the length of sensor's tie bar. Although the control procedure uses the data prior to feeding for the data in the period of material entering the bin, waggling of the body will be also caused after material enters the bin, the weighing accuracy of sensor will be directly affected, and thus the control procedure will also be influenced, therefore it is required to equip with a limit device at the lower part of bin, and this device shall not affect weighting.
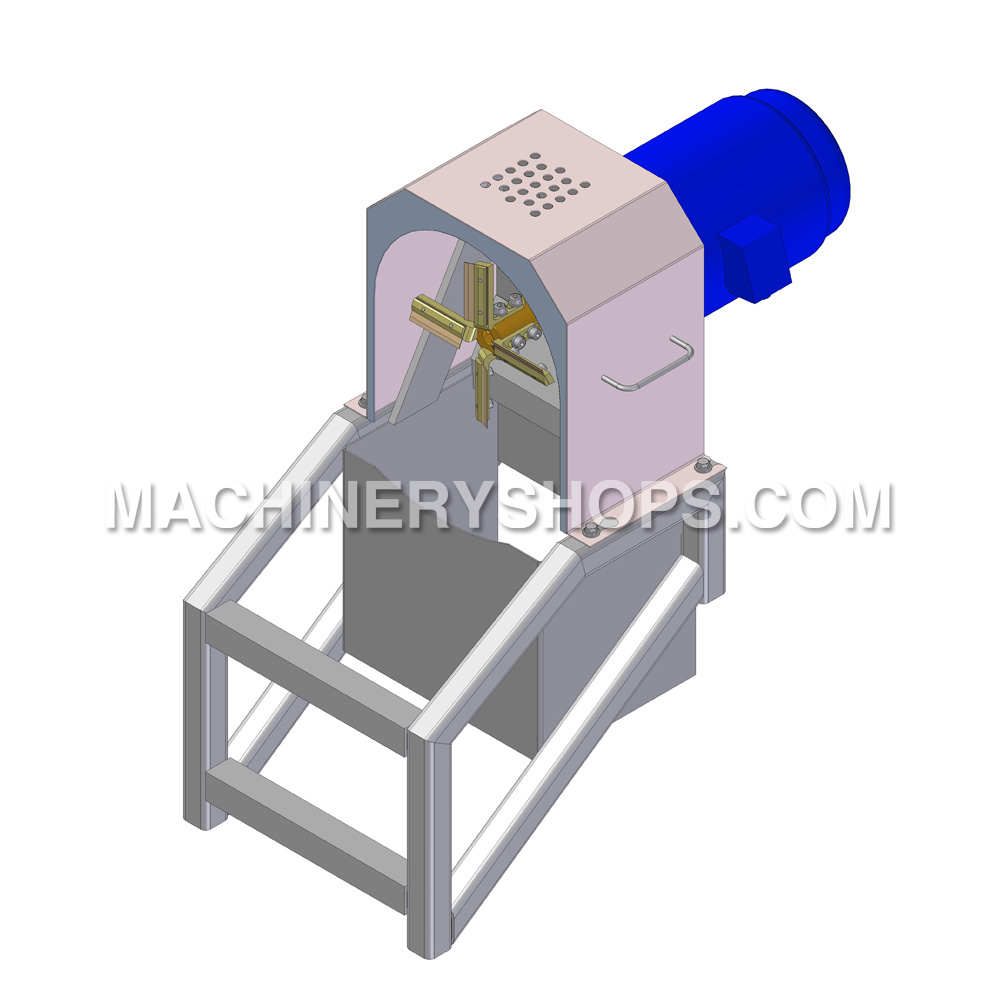
The another method is supporting installation, which will not cause waggling, but the whole bin body on the extruding machinery tends to translocation, therefore sensor should be fixed on a bracket during installation, and it is required to mount limit blocks at both sides of each ear of the feeding bin, so as to prevent the whole bin body from translocation.
It is necessary to pay attention to the position of access door during installation of bridge-breaking feeding bin, and the maintenance platform should be mounted at the lower part of access door while ensuring that the access door can be opened.
A basic requirement to the weighing feeding of the feed extruder is a flexible connection between upper and lower interface, namely, the flexible connection between bridge-breaking feeding bin and pneumatic gate at upper part of the bin, as well as the flexible connection between feeder outlet and conditioner inlet, canvas is usually used as the material for flexible connection for this two parts.
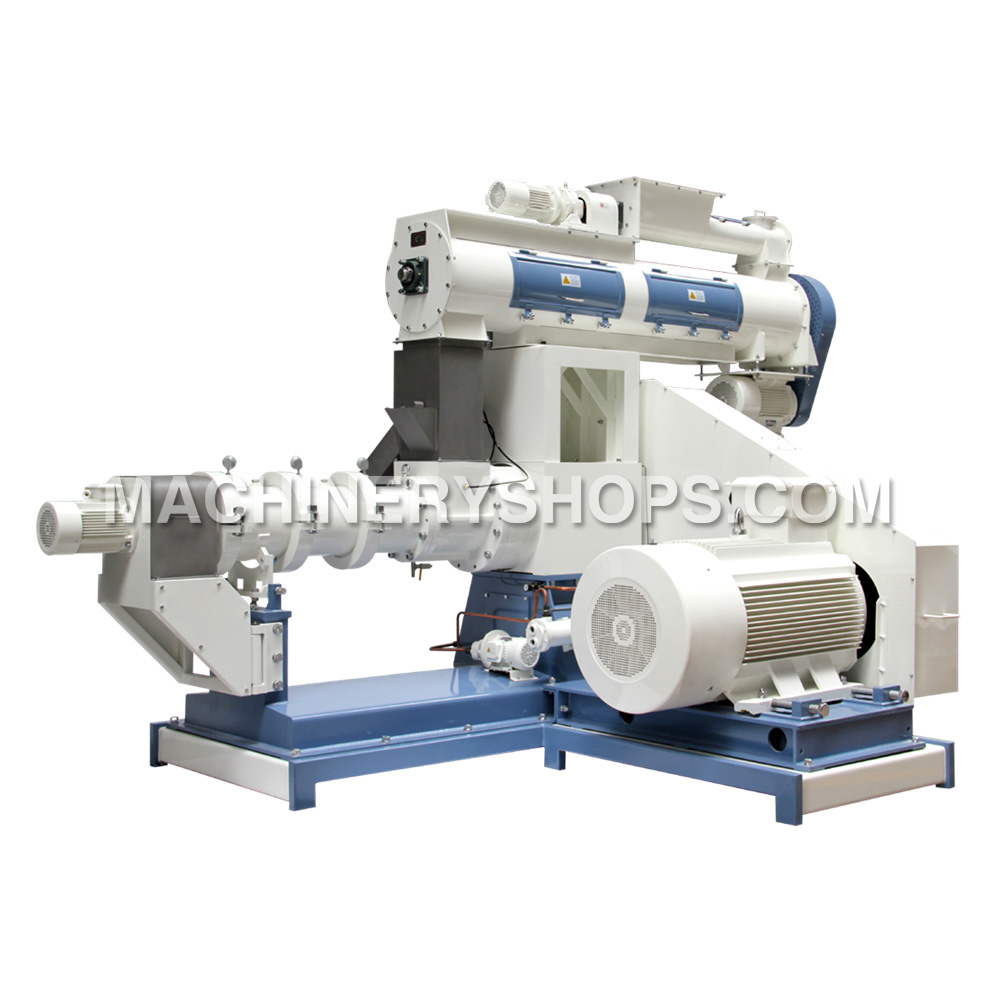
Installation of weighing sensor is another important factor affecting the feeding. There are generally two methods for sensor installation: hanging installation and supporting installation, which will be used as required in the site. Necessary measures shall be taken to ensure stability of bin body while hanging installation is used. During production of extruding machine, falling down of materials, when feeding to the feeding bin, will make the whole bin body waggled, the waggling extent and time will closely related to the length of sensor's tie bar. Although the control procedure uses the data prior to feeding for the data in the period of material entering the bin, waggling of the body will be also caused after material enters the bin, the weighing accuracy of sensor will be directly affected, and thus the control procedure will also be influenced, therefore it is required to equip with a limit device at the lower part of bin, and this device shall not affect weighting.
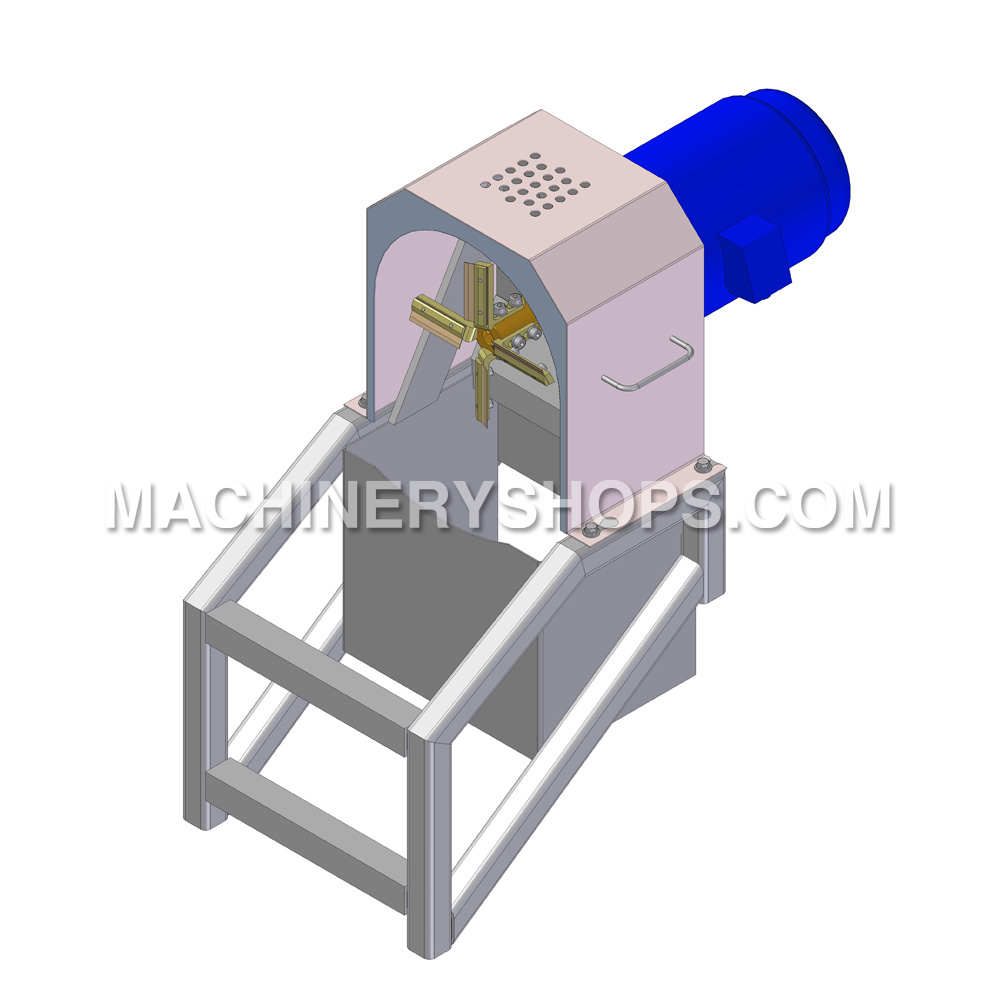
The another method is supporting installation, which will not cause waggling, but the whole bin body on the extruding machinery tends to translocation, therefore sensor should be fixed on a bracket during installation, and it is required to mount limit blocks at both sides of each ear of the feeding bin, so as to prevent the whole bin body from translocation.
It is necessary to pay attention to the position of access door during installation of bridge-breaking feeding bin, and the maintenance platform should be mounted at the lower part of access door while ensuring that the access door can be opened.
9/16/2013
Important Explanation on SWFP Series Fine-grinding Hammer Mill
Congratulations on your purchase of Muyang Brand Hammer mill. This design of Chaoyue Fine-Grinding Hammer Mill can both fulfill your requirements to grind different raw materials and also improve the material grinding efficiency. Prior to use, please read through this Operation Manual and well know the safety points, different performances, requirements to installation and operation etc. For this Hammer mill, so that you can expertly operate and use this machine, and create more benefits for you.
This Operation Manual shall be provided to your working personnel in charge of operating and managing the equipment manufactured by Jiangsu Muyang Group which is a successful grinding machine manufacturer. Therefore, it is very important to deliver these documents to them.

A check on appearance should be made immediately when the equipment is transported to the destination. If it is sure there is any damage caused during transport, a necessary claim procedure must be taken according to the supply contract. The repair expense shall be borne by relevant risk undertaker.
The grinding machine, which cannot be installed in predetermined place immediately, must be stored in a weatherproof place with facilities against external infringement in original packages. Any loss arising from storage shall be only conducted as per the principle specified in the Supply Contract.
The equipment and parts manufactured by Jiangsu Muyang Group shall be installed only by the trained technical personnel based on installation specifications provided together with the equipment.
If several structures on the grinding machinery are introduced in the documents provided, only the structures specified in Supply Contract shall be effective. We reserve the right of improvement before delivery.
Startup and commissioning shall only be done by trained personnel. The operators shall know the instructions and operation regulations in provided documents before startup. Lubricating oil shall be filled before startup, such as oil for variable speed devices.
The accident prevention rules in related documents must be well known and strictly obeyed. Jiangsu Muyang Group devotes to manufacturing machinery equipment according to the latest National Safety Standards (CE Certification Standards). Customers shall tell us the local safety rules before manufacturing. Additional expenses there from shall be borne by customers.
The leaders of an enterprise owning the equipment from Jiangsu Muyang Group shall have the duty to allow the operators to know the operating instructions, and shall point out where the especial dangers are during operating these grinding machines.
This Operation Manual shall be provided to your working personnel in charge of operating and managing the equipment manufactured by Jiangsu Muyang Group which is a successful grinding machine manufacturer. Therefore, it is very important to deliver these documents to them.

A check on appearance should be made immediately when the equipment is transported to the destination. If it is sure there is any damage caused during transport, a necessary claim procedure must be taken according to the supply contract. The repair expense shall be borne by relevant risk undertaker.
The grinding machine, which cannot be installed in predetermined place immediately, must be stored in a weatherproof place with facilities against external infringement in original packages. Any loss arising from storage shall be only conducted as per the principle specified in the Supply Contract.
The equipment and parts manufactured by Jiangsu Muyang Group shall be installed only by the trained technical personnel based on installation specifications provided together with the equipment.
If several structures on the grinding machinery are introduced in the documents provided, only the structures specified in Supply Contract shall be effective. We reserve the right of improvement before delivery.
Startup and commissioning shall only be done by trained personnel. The operators shall know the instructions and operation regulations in provided documents before startup. Lubricating oil shall be filled before startup, such as oil for variable speed devices.
The accident prevention rules in related documents must be well known and strictly obeyed. Jiangsu Muyang Group devotes to manufacturing machinery equipment according to the latest National Safety Standards (CE Certification Standards). Customers shall tell us the local safety rules before manufacturing. Additional expenses there from shall be borne by customers.
The leaders of an enterprise owning the equipment from Jiangsu Muyang Group shall have the duty to allow the operators to know the operating instructions, and shall point out where the especial dangers are during operating these grinding machines.
9/12/2013
Muyang Chaole Series SWFL 110B/C Ultra-fine Pulverizer
SWFL B/C series vertical ultra-fine pulverizer is a new type of equipment for large-, medium- and small-sized feed mills to process various coarse ground materials after preliminary cleaning, magnetic separation and mixing, such as corn, sorghum, rice, wheat, soybean meal, fish and shrimp, so as to obtain the materials in superfine particle size as required. It is especially suitable for fine grinding or ultra-fine grinding of feeds for prawn, turtle, eel and young animals.
SWFL B/C series ultra-fine grinding machine mainly consists of a stander, a grinding system, a grading system, a feeding system, a hydraulic opening mechanism as well as a main motor driving part for grinding and a motor driving part for grading (see Fig.1). The grinding system is composed of a main shaft, a grinding disc, a toothed ring and a grinding chamber; the grading system is composed of a grading impeller shaft, a grading impeller, a convex cover and a discharge chamber. The main motor runs in vertical driving way; the frequency conversion motors with frequency converters are used for both grading and feeding, so as to realize steeples speed regulation and remote control.

Preparation and inspection prior to first test run
1. Open the grading system, and check for any metal or sundries in the grinding chamber;
2. Check for any metal or sundries in the feeding bin or feeding screw;
3. All fasteners must be carefully checked for any looseness;
4. Check whether the driving belts are properly tensioned and the guard hood is well mounted;
5. Check each driving part on the grinding machinery for collision, analyzes the reason if any, and then put it right as soon as possible;
6. Turn each driving part and see whether there is any abnormality, and then inch each driving part and check whether they rotate in a correct direction;
a. The rotating direction of the grinding disc: clockwise in an overhead view.
b. The feeding screw: rightward.
c. Rotating direction of the grading impeller, normally it is clockwise in an overhead view. It can also be changed into counterclockwise according to actual situation.
7. Keep idle run of the hammer mill for 20-30 min. and observe its current, temperature and vibration: The temperature rise of the main shaft bearings should not exceed 35, and the maximum ℃temperature should not exceed 70 ℃(the ambient temperature should not exceed 40 ℃). The vibration amplitude of the machine should not be too large. And the machine cannot be loaded until it runs idly in a normal way.
8. During working, properly open the upper air gate of the gravity impurity removing chamber of the machine. And adjust the position of balance weight block on the gravity cover that is at the bottom of the machine so that it can open automatically when there are many impurities.
SWFL B/C series ultra-fine grinding machine mainly consists of a stander, a grinding system, a grading system, a feeding system, a hydraulic opening mechanism as well as a main motor driving part for grinding and a motor driving part for grading (see Fig.1). The grinding system is composed of a main shaft, a grinding disc, a toothed ring and a grinding chamber; the grading system is composed of a grading impeller shaft, a grading impeller, a convex cover and a discharge chamber. The main motor runs in vertical driving way; the frequency conversion motors with frequency converters are used for both grading and feeding, so as to realize steeples speed regulation and remote control.

Preparation and inspection prior to first test run
1. Open the grading system, and check for any metal or sundries in the grinding chamber;
2. Check for any metal or sundries in the feeding bin or feeding screw;
3. All fasteners must be carefully checked for any looseness;
4. Check whether the driving belts are properly tensioned and the guard hood is well mounted;
5. Check each driving part on the grinding machinery for collision, analyzes the reason if any, and then put it right as soon as possible;
6. Turn each driving part and see whether there is any abnormality, and then inch each driving part and check whether they rotate in a correct direction;
a. The rotating direction of the grinding disc: clockwise in an overhead view.
b. The feeding screw: rightward.
c. Rotating direction of the grading impeller, normally it is clockwise in an overhead view. It can also be changed into counterclockwise according to actual situation.
7. Keep idle run of the hammer mill for 20-30 min. and observe its current, temperature and vibration: The temperature rise of the main shaft bearings should not exceed 35, and the maximum ℃temperature should not exceed 70 ℃(the ambient temperature should not exceed 40 ℃). The vibration amplitude of the machine should not be too large. And the machine cannot be loaded until it runs idly in a normal way.
8. During working, properly open the upper air gate of the gravity impurity removing chamber of the machine. And adjust the position of balance weight block on the gravity cover that is at the bottom of the machine so that it can open automatically when there are many impurities.
9/11/2013
Major Component on MY56×2A Twin-Screw Extruder
Cutting device
As an important component, the cutting device has a great effect on the sustained and steady running of the extruder as well as the pellet form of expanding feed. The cutting device is mainly composed of a slide rail, housing, a screw moving device and a cutter driving unit, see Fig.3.7.
When working, slide the housing as well as the cutting driving device to the working place and fix. The cutter driving unit can be adjusted forward by turning the screw on the screw moving device when there is any wore on the cutter during working, which can ensure the clearance between the cutter blade and the die plate on the feed extruder keep appropriate. After working, the housing and cutter driving unit should be slide to the other side of the slide rail and then fixed.
Cutter driving unit
1. The driving component for cutting consists of cutting knives and a driving device with variable speed. A variable frequency speed control motor is applied for variable-speed driving; the cutting knife bar drives the cutting knives to rotate. The length of product to be cut is cont rolled by adjusting the rotating speed of the cutting knives.
2. There is a long hole in the knife support, through adjustment its position on the knife tray, the edge surface of knife can be in a surface.
Discharging device
In comparison with discharging device (I), a "8" shaped hole spacing plate is added in discharging device (II), and the others are the same except length of the screw.
The material extruded and ripened in extruder chamber must be formed through a discharging device and the discharging device is mainly used for limiting the flow of material to form the required pressure for expanded material at the end of expanding chamber. Structure of discharging device and selection of die can directly influence the quality of material.
The discharging assembly of this extruding machine mainly consists of "8" shaped bus bar and five die plates are available for this extruder.
Bypass
The bypass is located between outlet of different diameter cylinder conditioner and the inlet of extruding assembly. The flow direction of material from the conditioner can be selected through bypass: flow into inlet of extruding assembly for extrusion or flow out through chute of the bypass in convenience for checking conditioning efficiency of material.
As an important component, the cutting device has a great effect on the sustained and steady running of the extruder as well as the pellet form of expanding feed. The cutting device is mainly composed of a slide rail, housing, a screw moving device and a cutter driving unit, see Fig.3.7.

When working, slide the housing as well as the cutting driving device to the working place and fix. The cutter driving unit can be adjusted forward by turning the screw on the screw moving device when there is any wore on the cutter during working, which can ensure the clearance between the cutter blade and the die plate on the feed extruder keep appropriate. After working, the housing and cutter driving unit should be slide to the other side of the slide rail and then fixed.

Cutter driving unit
1. The driving component for cutting consists of cutting knives and a driving device with variable speed. A variable frequency speed control motor is applied for variable-speed driving; the cutting knife bar drives the cutting knives to rotate. The length of product to be cut is cont rolled by adjusting the rotating speed of the cutting knives.
2. There is a long hole in the knife support, through adjustment its position on the knife tray, the edge surface of knife can be in a surface.
Discharging device
In comparison with discharging device (I), a "8" shaped hole spacing plate is added in discharging device (II), and the others are the same except length of the screw.
The material extruded and ripened in extruder chamber must be formed through a discharging device and the discharging device is mainly used for limiting the flow of material to form the required pressure for expanded material at the end of expanding chamber. Structure of discharging device and selection of die can directly influence the quality of material.
The discharging assembly of this extruding machine mainly consists of "8" shaped bus bar and five die plates are available for this extruder.

Bypass
The bypass is located between outlet of different diameter cylinder conditioner and the inlet of extruding assembly. The flow direction of material from the conditioner can be selected through bypass: flow into inlet of extruding assembly for extrusion or flow out through chute of the bypass in convenience for checking conditioning efficiency of material.
Safety Specification for Operation of Pellet Mill
In order to ensure the safety of electric circuits and avoid explosion resulted from spark discharge, the paint coat at the electric connections must be removed, to make them earthed reliably.
General safety points
1. This machine shall be operated by trained and designated workers.
2. The main power supply must be cut off when making repairs and maintenance work, and it is forbidden to open the operation gate until the equipment is stopped fully.
3. When the machine is running, it is strictly forbidden to put fingers near the running parts, such work as inspection, maintenance and cleaning etc cannot be done until the rotor of Pellet Mill has completely stopped.
4. Wear protective gloves (max. temperature of ring die, press roller and other parts can be high up to 100℃), safety shoes with steel plate and safety helmets when making repairs and maintenance work.
5. It is not allowed to take off the guard for machine when running.
6. In case maintenance and inspection work should be done with a welder or other tools that can generate sparks, strict safety precautions must be taken against dust explosion and combustion.
7. The electric control device provided by Jiangsu Muyang Group is an integral part of the Accident Prevention Safety Plan, which shall be checked and approved in writing by experts of Muyang Group before startup. If any control system used for the equipment produced by Jiangsu Muyang Group is provided by a third party, it shall be manufactured according to the specifications of Muyang Group, and shall be checked carefully and approved in writing by an expert from Muyang Group before startup. If the control system for Muyang machinery equipment is not manufactured as per the quality standard, the Muyang Group will refuse to take any responsibility and the Group will reserve the right to investigate and affix the responsibility of the operator.
8. The interlocking limit switch is installed for opening the operation gate of Pellet Mill, the strict wiring must be ensured for cutting off the switch when opening the gate and the equipment cannot be started up after opening the operation gate. This safety device is concerned in life safety, so it may not be re moved or discarded, and shall be repaired or replaced immediately when any malfunction occurs.
9. Electric installation and the treatment of conducting parts can only be done by specialized persons in accordance with the national electric safety standards.
10. Keep the safety device in pelleting machine in good condition and regularly check its function, for instance once every month.
11. When the machine is under shutdown, attention must be taken to prevent it from being started by any starting mode.
12. Before the electric circuit is cut off, it is strictly prohibited to open the terminal box for avoiding electric shock.
General safety points
1. This machine shall be operated by trained and designated workers.
2. The main power supply must be cut off when making repairs and maintenance work, and it is forbidden to open the operation gate until the equipment is stopped fully.
3. When the machine is running, it is strictly forbidden to put fingers near the running parts, such work as inspection, maintenance and cleaning etc cannot be done until the rotor of Pellet Mill has completely stopped.
4. Wear protective gloves (max. temperature of ring die, press roller and other parts can be high up to 100℃), safety shoes with steel plate and safety helmets when making repairs and maintenance work.
5. It is not allowed to take off the guard for machine when running.
6. In case maintenance and inspection work should be done with a welder or other tools that can generate sparks, strict safety precautions must be taken against dust explosion and combustion.
7. The electric control device provided by Jiangsu Muyang Group is an integral part of the Accident Prevention Safety Plan, which shall be checked and approved in writing by experts of Muyang Group before startup. If any control system used for the equipment produced by Jiangsu Muyang Group is provided by a third party, it shall be manufactured according to the specifications of Muyang Group, and shall be checked carefully and approved in writing by an expert from Muyang Group before startup. If the control system for Muyang machinery equipment is not manufactured as per the quality standard, the Muyang Group will refuse to take any responsibility and the Group will reserve the right to investigate and affix the responsibility of the operator.
8. The interlocking limit switch is installed for opening the operation gate of Pellet Mill, the strict wiring must be ensured for cutting off the switch when opening the gate and the equipment cannot be started up after opening the operation gate. This safety device is concerned in life safety, so it may not be re moved or discarded, and shall be repaired or replaced immediately when any malfunction occurs.
9. Electric installation and the treatment of conducting parts can only be done by specialized persons in accordance with the national electric safety standards.
10. Keep the safety device in pelleting machine in good condition and regularly check its function, for instance once every month.
11. When the machine is under shutdown, attention must be taken to prevent it from being started by any starting mode.
12. Before the electric circuit is cut off, it is strictly prohibited to open the terminal box for avoiding electric shock.
9/09/2013
Countermeasures against Accidents --- From Muyang Group
1 All the mechanical equipments produced by Jiangsu Muyang Group are equipped with safety devices, which are consistent with modern technical level and universally effective safety rules prior to exworks, so that the customers can use the machines in accordance with the regulations.
2 Enterprises are obligate to execute following regulations to guarantee operators' safety.
3 The coupling shield cap must be mounted and closed at any moment. It is very dangerous to personal safety, if they are open or disassembled. This point is also applicable for the preventive device of manipulator.
4 The safety limit switch should always be kept in good order. The safety limit switch may not be overlapped or discarded.
5 The grating cover plate, grid bar or guard grating on the mixing machines are usually installed and delivered together with the machine. They can only be disassembled with tools. And the machines with such kind of devices can be never put into work until the above-said devices have been properly installed.
6 The driving motor must be switched off completely when carrying out inspection, commissioning, repair and maintenance. This can be realized through a full-phase separating and lockable switch installed near the machine or on the operation desk and control panel on the site. It is not enough only to screw off the fuse wire!
7 If the machines need other energy like pneumatic, hydraulic, steam and hot water energy, it is necessary to cut off their energy supply or turn off the switch, and eliminate the pressure in the internal pipeline system of the machine.
8 As for handling heated or cooled parts and components of the pelleting machine, especial care should still be taken for the danger of burning possibility.
9 If you have pressed the emergency stop switch to stop the machine and you want to reset the switch, so it is not permissible to only re-press this button to restart the machine. And the machine can only be started by re-closing the main switch first.
10 If some machines are equipped with a local shutdown system, especial care should be taken. Read the instruction manuals attached with the machine carefully. In such machines with a local shutdown system, temperature will rise because of pressure or vacuum will occur after they have been used for a period.
11 If the operators employed cannot read or write, the owner has the duty to explain to them clearly where dangers exist and warn them that special attention should be paid.
12 The cleaning, lubricating and oiling of the grinding machine or its parts and components may be carried out only when the machine is stopped. If you must climb on or enter the machine to do such work, the mandatory provisions shall be made without exception: the power supply of motors must be cut off completely and the switch must be locked.
13 Be careful, sampling from inside the machine can never be carried out unless there is not any danger. Usually, the samples can be taken from the pipe under the machine instead of inside machine.
14 Clear off the deposited dust, dirties and materials frequently. Keeping the machine clean can enhance production safety and the cleaning level of workshop, and is also beneficial to dust explosion prevention.
15 If oil (grease) leakage occurs, clean it immediately and seal well the place where leakage occurs, and for oil or grease leaked on the floor will easily bring about hazards to the operator.
16 In production operation, the machine must be equipped with safety devices, which may be neither removed and abandoned nor reduced in functions. Otherwise, we are not responsible for any accidents resulted here from, and reserve the right to ascertain where the responsibility lies.
17 Please execute the special regulations on accidents prevention in the operating instructions provided us.
18 Only the trained professionals are allowed to operate the machine and equipment manufactured by Muyang.
19 Measures for environmental protection
If you decide not to use the machine any longer, the measures for environmental protection and reutilization should be taken: drain the liquids inside the extruder machine (like motor oil, gearbox oil, brake oil and coolant etc.) into special containers and send them to the preparation workshop. The plastic parts shall be picked out for reutilization. The metal parts shall be sorted out so as to be crushed or scraped.
2 Enterprises are obligate to execute following regulations to guarantee operators' safety.
3 The coupling shield cap must be mounted and closed at any moment. It is very dangerous to personal safety, if they are open or disassembled. This point is also applicable for the preventive device of manipulator.
4 The safety limit switch should always be kept in good order. The safety limit switch may not be overlapped or discarded.
5 The grating cover plate, grid bar or guard grating on the mixing machines are usually installed and delivered together with the machine. They can only be disassembled with tools. And the machines with such kind of devices can be never put into work until the above-said devices have been properly installed.
6 The driving motor must be switched off completely when carrying out inspection, commissioning, repair and maintenance. This can be realized through a full-phase separating and lockable switch installed near the machine or on the operation desk and control panel on the site. It is not enough only to screw off the fuse wire!
7 If the machines need other energy like pneumatic, hydraulic, steam and hot water energy, it is necessary to cut off their energy supply or turn off the switch, and eliminate the pressure in the internal pipeline system of the machine.
8 As for handling heated or cooled parts and components of the pelleting machine, especial care should still be taken for the danger of burning possibility.
9 If you have pressed the emergency stop switch to stop the machine and you want to reset the switch, so it is not permissible to only re-press this button to restart the machine. And the machine can only be started by re-closing the main switch first.
10 If some machines are equipped with a local shutdown system, especial care should be taken. Read the instruction manuals attached with the machine carefully. In such machines with a local shutdown system, temperature will rise because of pressure or vacuum will occur after they have been used for a period.
11 If the operators employed cannot read or write, the owner has the duty to explain to them clearly where dangers exist and warn them that special attention should be paid.
12 The cleaning, lubricating and oiling of the grinding machine or its parts and components may be carried out only when the machine is stopped. If you must climb on or enter the machine to do such work, the mandatory provisions shall be made without exception: the power supply of motors must be cut off completely and the switch must be locked.
13 Be careful, sampling from inside the machine can never be carried out unless there is not any danger. Usually, the samples can be taken from the pipe under the machine instead of inside machine.
14 Clear off the deposited dust, dirties and materials frequently. Keeping the machine clean can enhance production safety and the cleaning level of workshop, and is also beneficial to dust explosion prevention.
15 If oil (grease) leakage occurs, clean it immediately and seal well the place where leakage occurs, and for oil or grease leaked on the floor will easily bring about hazards to the operator.
16 In production operation, the machine must be equipped with safety devices, which may be neither removed and abandoned nor reduced in functions. Otherwise, we are not responsible for any accidents resulted here from, and reserve the right to ascertain where the responsibility lies.
17 Please execute the special regulations on accidents prevention in the operating instructions provided us.
18 Only the trained professionals are allowed to operate the machine and equipment manufactured by Muyang.
19 Measures for environmental protection
If you decide not to use the machine any longer, the measures for environmental protection and reutilization should be taken: drain the liquids inside the extruder machine (like motor oil, gearbox oil, brake oil and coolant etc.) into special containers and send them to the preparation workshop. The plastic parts shall be picked out for reutilization. The metal parts shall be sorted out so as to be crushed or scraped.
9/05/2013
MY56×2A Twin-Screw Extruder
The extruder is mainly composed of a feeder, a different diameter cylinder conditioner, an extruding device, simple pipeline system and electric control, see following picture.

The feeder is mainly used for feeding the material to conditioner in a certain amount, the equipped motor is of the frequency conversion speed control motor, and the rotation speed can be adjusted based on actual production situation.
The feeder of the extruding machinery is mainly composed of a convertor motor, a feeding bin, an anti-bridge device, a screw conveying device and a discharging out let, see following picture. The working procedure is: material in the feeding bin is pulled forward along the axial of the screw conveying device by the convertor motor, and then drop into the conditioner through the discharging outlet. At the same time, the anti-bridge shaft drove by the chain is rotating in the feeding bin to prevent generating blockage.

The conditioner on the extruding machine is made of complete stainless steel and mainly composed of a speed reducer motor, a feeding inlet, a water inlet, a steam inlet, a stirring shaft, a conditioning cylinder and a discharging outlet. Main features are shown as follows: two agitator shafts with different diameters and rotation speeds agitate the material through back cross movement, the agitation efficiency is good at that the material, steam, water or other liquid can be sufficiently mixed; and a housing with large volume is used so that the material can be kept long enough under a certain temperature and moisture content in the conditioner on the purpose for ripening.

Advantages of conditioning:
a. The production capacity can be improved.
The partially cooking material with steam needs a very less mechanical energy for heating products to the maximum temperature, therefore, as for a device with designated power, and the production capacity is greater than dry feed extruder with the same power.
b. The forming capability is greater.
The use of steam and water can make the water content of material be improved, and this will greatly improve the forming performance and final quality of the products.
c. The abrasion of extruding parts is reduced.
The cooked material has the corresponding temperature and ripeness, therefore, too much higher pressure and abrasion in the machine chamber are not required, and also the water can be used for lubricating, these can greatly reduce abrasion, so that service life of machine chamber and screw can be increased.
d. The gelatinization of product can be improved.
The steam cooking can improve gelatinization of produce, make it more taste and easier for absorption.

The feeder is mainly used for feeding the material to conditioner in a certain amount, the equipped motor is of the frequency conversion speed control motor, and the rotation speed can be adjusted based on actual production situation.
The feeder of the extruding machinery is mainly composed of a convertor motor, a feeding bin, an anti-bridge device, a screw conveying device and a discharging out let, see following picture. The working procedure is: material in the feeding bin is pulled forward along the axial of the screw conveying device by the convertor motor, and then drop into the conditioner through the discharging outlet. At the same time, the anti-bridge shaft drove by the chain is rotating in the feeding bin to prevent generating blockage.

The conditioner on the extruding machine is made of complete stainless steel and mainly composed of a speed reducer motor, a feeding inlet, a water inlet, a steam inlet, a stirring shaft, a conditioning cylinder and a discharging outlet. Main features are shown as follows: two agitator shafts with different diameters and rotation speeds agitate the material through back cross movement, the agitation efficiency is good at that the material, steam, water or other liquid can be sufficiently mixed; and a housing with large volume is used so that the material can be kept long enough under a certain temperature and moisture content in the conditioner on the purpose for ripening.

Advantages of conditioning:
a. The production capacity can be improved.
The partially cooking material with steam needs a very less mechanical energy for heating products to the maximum temperature, therefore, as for a device with designated power, and the production capacity is greater than dry feed extruder with the same power.
b. The forming capability is greater.
The use of steam and water can make the water content of material be improved, and this will greatly improve the forming performance and final quality of the products.
c. The abrasion of extruding parts is reduced.
The cooked material has the corresponding temperature and ripeness, therefore, too much higher pressure and abrasion in the machine chamber are not required, and also the water can be used for lubricating, these can greatly reduce abrasion, so that service life of machine chamber and screw can be increased.
d. The gelatinization of product can be improved.
The steam cooking can improve gelatinization of produce, make it more taste and easier for absorption.
9/03/2013
Muyang SFSP112CB Series Hammer Mill
The SFSP112C/B、SFSP56C series mill developed independently by Muyang group are capable for grinding various raw materials, such as corn, kaoliang, wheat and crushed cakes etc. They are widely used for grinding granular raw material in various livestock feed mills, aqua feed mills, alcohol plants, lemon plants, food factories and edible oil mills.
Main features and functions on the grinding machinery
(1) Fully optimized hammers arrangement and adjustable clearance between hammers and screen.
(2) Various tests including high-precise dynamic balancing ensure much stable running, lower noise and better performance.
(3) The rotor that rotates in forward and backward direction can increase the service life of wearing parts.
(4) The displaceable and fully operable access door and the interlocked sieve hold-down fixture make the operation more convenient.
(5) The machine can be equipped with advanced impeller feeder with frequency conversion or magnetic belt feeder make the working performance more reliable.
Main structure
As a powerful grinding machine manufacturer, Muyang has made its machines with high quality. Being a sort of welded steel structure, the hammer mill consists of a base, an upper housing, a rotor, an excess door, a sieve hold-down fixture, a feed guiding device and etc. The inlet and outlet locate at top and bottom centers respectively. The driving motor and the rotor are mounted on a same base, and direct driving is realized by means of an elastic pin shaft coupling.
Main features and functions on the grinding machinery
(1) Fully optimized hammers arrangement and adjustable clearance between hammers and screen.
(2) Various tests including high-precise dynamic balancing ensure much stable running, lower noise and better performance.
(3) The rotor that rotates in forward and backward direction can increase the service life of wearing parts.
(4) The displaceable and fully operable access door and the interlocked sieve hold-down fixture make the operation more convenient.
(5) The machine can be equipped with advanced impeller feeder with frequency conversion or magnetic belt feeder make the working performance more reliable.
Main structure
As a powerful grinding machine manufacturer, Muyang has made its machines with high quality. Being a sort of welded steel structure, the hammer mill consists of a base, an upper housing, a rotor, an excess door, a sieve hold-down fixture, a feed guiding device and etc. The inlet and outlet locate at top and bottom centers respectively. The driving motor and the rotor are mounted on a same base, and direct driving is realized by means of an elastic pin shaft coupling.
Subscribe to:
Posts (Atom)